
Brand | KMCable |
---|---|
code | Multi-Core |
Conductor | copper |
Nominal voltage U0/U | 300V/500V |
Temperature (°C) - flexing | -5 to +80℃ |
Temperature (°C) - fixed | -40 to +80℃ |
Color | Gray |
MOQ | 500meter |
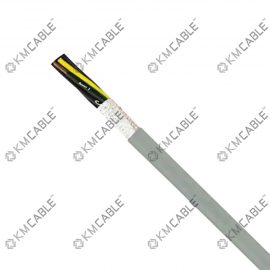
Brand | KMCable |
---|---|
code | Multi-Core |
Conductor | copper |
Nominal voltage U0/U | U0/U 300/500 V |
Temperature (°C) - flexing | -10°C to +80°C |
Temperature (°C) - fixed | -40 to +80℃ |
Color | Gray |
MOQ | 500meter |
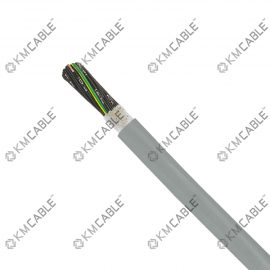
Brand | KMCable |
---|---|
code | Multi-Core |
Conductor | copper |
Nominal voltage U0/U | U0/U 300/500 V |
Temperature (°C) - flexing | -10°C to +80°C |
Temperature (°C) - fixed | -40 to +80℃ |
Color | Gray |
MOQ | 500meter |

Brand | KMCable |
---|---|
code | Multi-Core |
Conductor | copper |
Nominal voltage U0/U | U0/U 300/500 V |
Temperature (°C) - flexing | -10°C to +80°C |
Temperature (°C) - fixed | -40 to +80℃ |
Color | Gray |
MOQ | 500meter |
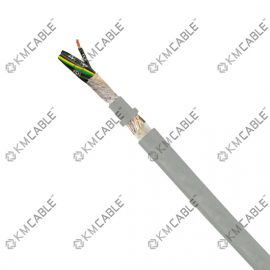
Brand | KMCable |
---|---|
code | Multi-Core |
Conductor | copper |
Nominal voltage U0/U | U0/U 300/500 V |
Temperature (°C) - flexing | -10°C to +80°C |
Temperature (°C) - fixed | -40 to +80℃ |
Color | Gray |
MOQ | 500meter |
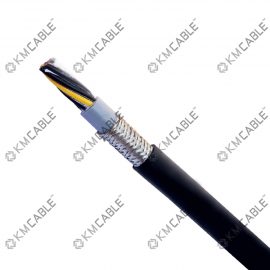
Brand | KMCable |
---|---|
code | Multi-Core |
Conductor | copper |
Nominal voltage U0/U | U0/U 300/500 V |
Temperature (°C) - flexing | -15°C to +80°C |
Temperature (°C) - fixed | -30ºC to +80ºC |
Color | Black |
MOQ | 500meter |
Drag chain cable
In the world of machinery setups, cable management is a crucial aspect that often gets overlooked. Unruly cables not only pose safety hazards but can also lead to operational inefficiencies and increased downtime. Enter drag chain cables – a revolutionary solution designed to enhance cable management in dynamic environments. In this blog post, we’ll delve into the best practices for mastering cable management using drag chain cables, while also highlighting the numerous benefits they bring to machinery setups.
The Basics of Drag Chain Cables
Drag chain cables, also known as cable carriers or energy chains, are specially designed to withstand constant movement and bending in machinery setups. They are commonly used in applications where traditional cables may fail due to wear and tear caused by repetitive motion. Drag chain cables are constructed with a durable outer shell that protects the internal cables from external factors, ensuring reliable and long-lasting performance.
Tips for Effective Installation
- Choose the Right Type of Drag Chain Cable: Selecting the appropriate type of drag chain cable for your specific application is the first step towards effective cable management. Consider factors such as the type of movement, speed, and environmental conditions to determine the most suitable cable for your machinery.
- Proper Sizing and Length: Ensure that the drag chain cable is correctly sized and cut to the appropriate length. Proper sizing prevents excessive stress on the cables and reduces the risk of damage during movement. Measure the distance the cables need to travel and account for any additional slack required for flexing and bending.
- Secure Mounting: Securely mount the drag chain system to the machinery, ensuring that it moves smoothly without any obstructions. Adequate support prevents sagging and minimizes the risk of cables getting caught or damaged during operation.
- Regular Inspection and Maintenance: Implement a routine inspection and maintenance schedule to identify any signs of wear, damage, or fatigue. Promptly replace any damaged cables to prevent potential disruptions and extend the overall lifespan of the drag chain system.
Benefits of Drag Chain Cables
- Enhanced Cable Protection: Drag chain cables provide a protective shield around internal cables, guarding them against abrasion, oils, chemicals, and other environmental factors. This enhanced protection contributes to the longevity and reliability of the cables.
- Increased Operational Lifespan: The robust construction of drag chain cables allows them to withstand constant movement and bending, resulting in a longer operational lifespan compared to traditional cables. This durability translates to reduced downtime and maintenance costs.
- Improved Safety: Proper cable management with drag chain cables reduces the risk of accidents caused by tripping hazards or cable damage. This, in turn, enhances the overall safety of the machinery setup and the working environment.
- Optimized Performance: Drag chain cables facilitate smooth and controlled cable movement, optimizing the performance of machinery setups. The reduction of cable stress and wear ensures consistent signal transmission and power supply, leading to improved efficiency.
Mastering cable management is essential for the seamless operation of machinery setups, and drag chain cables offer an effective solution to this challenge. By following the best practices outlined above, businesses can ensure the proper installation and maintenance of drag chain cables, reaping the benefits of enhanced cable protection, increased operational lifespan, improved safety, and optimized performance. Investing in drag chain cables is not just a practical choice; it’s a strategic move towards a more efficient and reliable industrial environment.
Categories
- 0.6/1 kv Power Cable (17)
- LS0H/LSZH cable (2)
- PVC Cable (3)
- Rubber Cable (9)
- XLPE cable (4)
- Automotive wire (39)
- American standard wire (9)
- Car Battery Cable (34)
- Euro standard wire (12)
- EV Cable (8)
- Japanese standard wire (7)
- Coil cable (34)
- PUR cable (12)
- PVC cable (3)
- Rubber cable (9)
- Spiral cable assembly (10)
- Flexible control cable (2)
- Genie Parts (5)
- Industrial Wire Cable (33)
- CCC wire (5)
- CE Cable (3)
- Data cable (6)
- Drag chain cable (7)
- Robot cable (2)
- Servo cable (3)
- Special cable (3)
- UL wire (3)
- Media Cable (5)
- Microphone Cable (1)
- Speaker cable (4)
- Other (4)
- Ready to Ship (23)
- Single Core Cable (21)
- CE certificated cable (7)
- Drag chaine cable (2)
- Photovoltaic cable (5)
- PUR flexible cable (3)
- Solar Cable (7)
- UL certificated cable (3)
- Trailer Truck Cable (26)
- Coil Cable Assembly (16)
- Trailer cable (10)
- Wire harness for industry (7)
Producer
Price
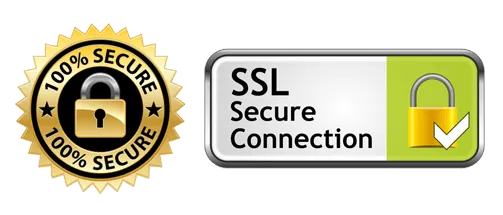
As direct sale from our factory, we offer bellow benefits:
- Best price on the market guaranteed !
- The option to modify the product, such as the color, the length, you name it!