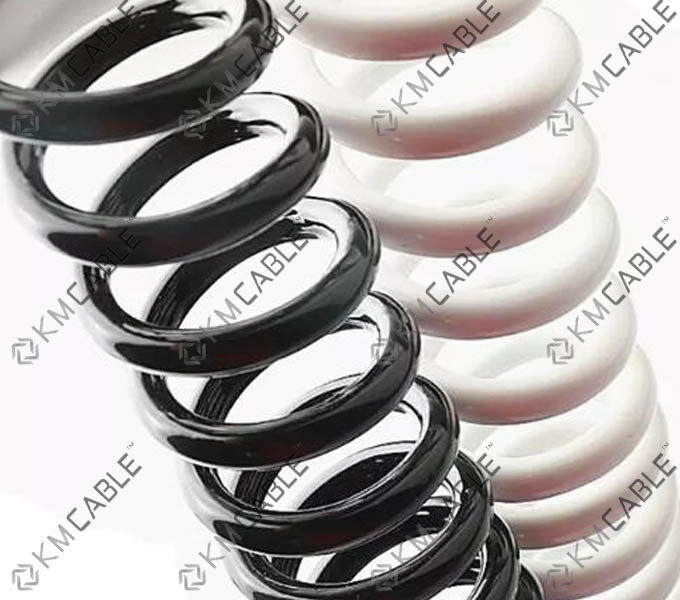
Wire harnesses are essential components in various electrical systems, serving as organized bundles of wires and cables that transmit signals and power between different parts of a machine or system. They provide a streamlined and organized way to manage complex electrical connections, ensuring both reliability and ease of maintenance.
The importance of selecting the right wire harness cannot be overstated, especially when dealing with high-performance applications in industries like automotive, industrial manufacturing, and medical equipment. Inadequate harness selection can lead to electrical failures, reduced efficiency, and safety risks. This guide will help you understand the key features and considerations for choosing the appropriate wire harness for your specific needs.
Understanding the Role of Wire Harnesses in Different Industries
Automotive
In automotive applications, wire harnesses play a critical role in ensuring that various systems, such as lighting, engine control, infotainment, and safety systems, operate seamlessly. The harness must withstand extreme conditions, including temperature fluctuations, vibrations, and exposure to chemicals and moisture.
Industrial
For industrial applications, wire harnesses are used in machinery, robotics, and automation systems. These environments often demand heavy-duty harnesses that can handle high power loads and endure tough operating conditions, such as exposure to corrosive chemicals, high humidity, and mechanical stress.
Medical
Medical equipment requires wire harnesses that meet strict regulatory standards for safety, cleanliness, and precision. These harnesses are used in devices like MRI machines, patient monitors, and surgical equipment, where even minor failures could jeopardize patient safety.
Key Factors to Consider When Selecting a Wire Harness
To select the best wire harness for any application, it’s important to consider several factors:
Electrical Requirements
– Voltage and Current Ratings: The harness must support the required electrical loads without overheating or causing signal interference.
– Signal Integrity: In sensitive applications, such as medical devices, the harness must maintain signal integrity, avoiding any electromagnetic interference (EMI).
Environmental Conditions
– Temperature Range: High-performance harnesses for automotive or industrial settings must tolerate extreme temperatures.
– Exposure to Moisture or Chemicals: Harnesses in industrial environments should be resistant to moisture, oils, and corrosive chemicals.
Durability and Longevity
– Mechanical Stress: The harness must withstand vibrations, impacts, and flexing, especially in automotive and industrial environments.
– Lifespan: For critical applications, the wire harness should offer a long lifespan with minimal risk of failure.
Regulatory Compliance
– Industry Standards: Wire harnesses must meet specific industry standards, such as ISO or UL certifications, depending on the application.
Wire Harnesses for Automotive Applications
Wire harnesses in the automotive industry are exposed to harsh conditions, including extreme heat, vibration, and exposure to various fluids. To ensure performance and safety, automotive wire harnesses must possess several key features:
High-Temperature Resistance
The engine compartment and exhaust systems can expose wire harnesses to very high temperatures. Materials like cross-linked polyethylene (XLPE) or Teflon are often used for insulation to withstand such conditions.
Vibration and Impact Resistance
Automobiles experience significant vibrations and shocks, especially in off-road or performance vehicles. Wire harnesses must be designed with high mechanical resilience, often incorporating strain reliefs or flexible materials to prevent wire fatigue.
Flexibility and Compact Design
Modern vehicles are increasingly compact, requiring flexible and space-efficient wire harnesses that can fit into tight spaces while still maintaining electrical integrity.
Wire Harnesses for Industrial Applications
In industrial settings, wire harnesses must handle more extreme environmental and mechanical stress than in other industries. Whether for factory automation systems, heavy machinery, or robotic arms, the wire harness needs to be robust and adaptable.
Heavy-Duty Construction
Industrial wire harnesses often require heavy-duty construction, using materials that can withstand high mechanical stress, such as reinforced insulation and rugged outer jackets.
Chemical and Moisture Resistance
Exposure to chemicals, oils, and moisture is common in industrial environments. Wire harnesses need to be resistant to these elements, with specific material coatings like PVC or silicone to prevent degradation.
Customization for Complex Systems
Many industrial applications involve highly specialized equipment with unique configurations. Custom wire harnesses are often necessary to ensure the correct fit and function within these systems.
Wire Harnesses for Medical Equipment
Medical applications demand wire harnesses that meet the highest safety and performance standards due to the critical nature of the equipment. Factors like precision, reliability, and sterilization are crucial.
High Precision and Safety Standards
Medical wire harnesses are designed to carry precise signals for life-saving equipment. Any failure in the electrical connection can lead to malfunctions in devices like ventilators or defibrillators, potentially endangering lives.
Sterilization and Cleanroom Compatibility
Medical harnesses must often be sterilized to ensure they are free from contaminants. Materials used must withstand sterilization processes, such as autoclaving, without degrading.
Biocompatibility and EMI Shielding
In applications like implantable devices or sensitive diagnostic equipment, wire harnesses must be biocompatible and offer protection from electromagnetic interference (EMI), which could disrupt medical readings or device performance.
Material Selection for Wire Harnesses
Choosing the right materials is critical for ensuring the longevity and performance of wire harnesses. This includes the insulation, conductors, and any shielding needed.
Insulation Materials
– PVC: Common and cost-effective, but not ideal for high temperatures.
– Teflon: Excellent for high-temperature and chemical-resistant applications.
– Silicone: Flexible and used in medical or high-vibration environments.
Conductor Materials
– Copper: The most common and effective conductor due to its high conductivity.
– Aluminum: Lighter than copper but with lower conductivity, sometimes used in automotive applications.
Shielding Options
Shielding is necessary to protect sensitive signals from EMI, especially in medical and automotive applications. Options include braided wire or metal foil.
Connectors and Terminations: Ensuring Reliable Performance
The connectors and terminations used in a wire harness are just as important as the wires themselves, as they ensure stable and reliable connections between components.
Types of Connectors
– Automotive: Often use waterproof or high-temperature resistant connectors.
– Industrial: Heavy-duty connectors that can withstand harsh environments.
– Medical: Precision connectors with EMI shielding and sterilizable materials.
Termination Methods
Crimping, soldering, or ultrasonic welding are common termination methods, depending on the application’s durability and electrical needs.
Custom vs. Off-the-Shelf Wire Harnesses
Choosing between custom-made and off-the-shelf wire harnesses depends on the specific needs of your application.
When to Choose Custom Wire Harnesses
– Complex Systems: Custom harnesses are often necessary for complex or unique systems, such as advanced medical devices or specialized industrial equipment.
Benefits of Off-the-Shelf Solutions
Cost-Effective: Off-the-shelf harnesses are generally more affordable and sufficient for less demanding applications.
Testing and Quality Assurance
Regardless of the application, wire harnesses must undergo rigorous testing to ensure they meet the required standards for performance and safety.
Electrical Testing
Testing for continuity, insulation resistance, and high-voltage performance ensures that the wire harness functions correctly.
Environmental Testing
Wire harnesses for industrial or automotive applications should undergo environmental tests
to ensure durability under extreme conditions.
Cost vs. Performance: Finding the Right Balance
While it might be tempting to choose the most affordable option, balancing cost with performance is crucial. Investing in a high-quality wire harness can prevent costly failures down the line, especially in critical applications like medical devices.
Common Mistakes to Avoid When Selecting Wire Harnesses
– Ignoring Environmental Conditions: Failing to consider the environmental challenges the harness will face can lead to premature failures.
– Overlooking Certification Requirements: Always ensure the wire harness complies with industry-specific standards.
Partnering with the Right Supplier or Manufacturer
Selecting a reliable wire harness manufacturer is just as important as choosing the right product. Look for suppliers with experience in your industry and a strong track record of quality and compliance.
Choosing the right wire harness for your application requires careful consideration of electrical, environmental, and regulatory factors. Whether you’re designing systems for the automotive, industrial, or medical sectors, selecting a harness that meets your specific needs ensures reliability, safety, and long-term performance.
For optimal results, work closely with your wire harness manufacturer to ensure your harness is designed and tested for the demands of your application.